Produktionsdaten und personenbezogene Daten
Lektion 4
Der magische Handschuh
Lisa ist beeindruckt, wie reibungslos die Zusammenarbeit von Mensch und Maschine in der Smart Factory funktioniert. Im Kleinen kennt sie das auch aus ihrem Ausbildungsbetrieb. Dort arbeiten sie mit einer Software, um Sensordaten von Autos auszulesen. Sie muss sich nur einloggen und schon kann sie die Software nutzen.
Auch die Roboter „wissen“ sofort, mit wem sie zusammenarbeiten, wenn man sich einloggt. Lisa findet es praktisch, dass die Maschine die Arbeitenden wiedererkennt und jeden Arbeitsschritt dokumentiert.
Omar dämpft ihre Begeisterung allerdings. Viele seiner Kolleg*innen waren zu Beginn skeptisch: Grenzt es nicht schon an totale Überwachung, wenn sich auslesen lässt, wer wann welche Arbeitsschritte ausgeführt hat?
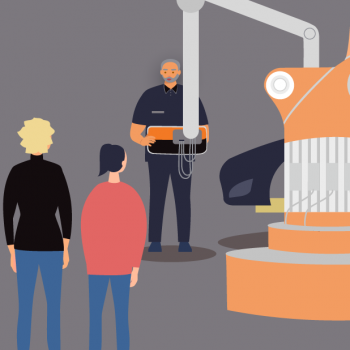
Omar zieht sich nun einen Handschuh über, auf dem eine Art Scanner befestigt ist. Mit diesem Datenhandschuh kann er die Strichcodes von Bauteilen scannen, bevor er sie aus einem Fach nimmt. Sie werden dann automatisch aus dem Lagerbestand ausgebucht, das Fach wird neu befüllt und das ERP-System bestellt zum passenden Zeitpunkt Teile nach.
Omar muss zwar im System angemeldet sein, aber sein Name wird nicht mit den anderen Daten verknüpft und die Daten werden nach einem festgelegten Zeitraum wieder gelöscht. Darauf achten die Datenschutzbeauftragten der Smart Factory.
Lisa überlegt, dass sie das ihrem Chef in der Werkstatt vorschlagen müsste, denn manchmal kennt niemand den genauen Lagerbestand.
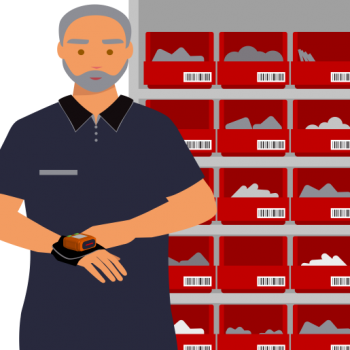
Zeit für eine Pause
Omar zeigt Lisa ein Beispiel, wie die Daten des Scanner-Handschuhs von einer Software visualisiert werden können. Die Frage war, wie viele Pausen Arbeiter*innen benötigen, damit es ihnen gut geht und auch die Qualität der Arbeit stimmt.
Dafür hatte die Qualitäts-Arbeitsgruppe auswerten lassen, wie sich die Montagedauer für ein Bauteil mit der Zeit verändert. Solche Daten nennt man Zeitreihe: Der Punkt ganz links zeigt die Montagedauer für das erste Teil, der Punkt ganz rechts die Dauer für das zweihundertste Teil.
Die Theorie war, dass man problemlos 100 Teile hintereinander montieren kann. Aber die Grafik hat Zweifel geweckt: Es scheint, dass die Montagedauer bereits nach 50 Teilen zu schwanken beginnt und sich verlängert.
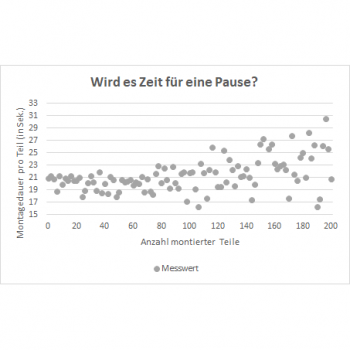
Mit einem Algorithmus wertet die Software die Montagezeit der ersten 50 Teile aus. Auf dieser Grundlage ermittelt sie den statistischen Normalbereich. Das ist der Bereich, in dem 95 Prozent der Montagezeiten liegen.
Die Software zeichnet diesen Normalbereich dann als blaue Linien in die Grafik ein. Damit lässt sich deutlich erkennen, dass tatsächlich schon nach etwa 50 montierten Teilen die Montagezeiten stärker schwanken und immer länger dauern.
Woran liegt das? Vielleicht lässt die Aufmerksamkeit der Arbeiter*innen im Laufe der Zeit einfach nach, weil sie sich ja doch sehr konzentrieren müssen?
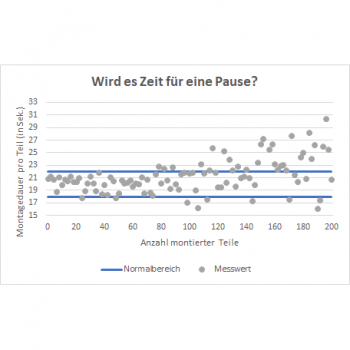
Aufgabe
Hast du gut aufgepasst? Dann teste dein Wissen!
Die Datenanalyse habe dem Team die Augen geöffnet, sagt Omar. Nun sollen Pausenzeiten früher eingeplant werden. Weil die erhobenen Daten zu den Montagezeiten nicht bei allen Mitarbeiter*innen gleich aussehen, überlegt die Arbeitsgruppe auch, ob individuelle Arbeitsunterbrechungen sinnvoller sind.
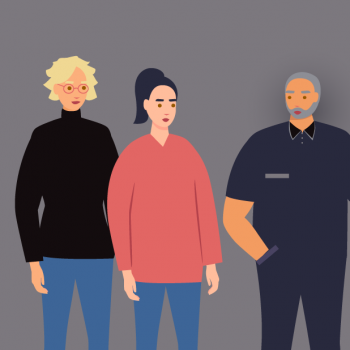
Schützende Sensoren
Ein Datenhandschuh liefert Daten, die die Produktionsabläufe effektiver machen. Autonome Warenlager „wissen“ so im Voraus, wann ein Werkstück benötigt wird, weil mit Algorithmen und den Daten eine Prognose über die nächste Entnahme erstellt wird.
Man kann so aber auch den Arbeitsschutz verbessern: Daten über genaue Positionen und Bewegungen von Menschen in der Fabrik können etwa helfen, Unfälle zu vermeiden. Ungeplante Begegnungen mit einem Roboter können gefährliche Folgen haben, deshalb berechnen Algorithmen, wann eine Kollision droht. Eine Steuerungssoftware sendet dem Roboter dann ein Signal, anzuhalten oder sich wegzubewegen, bevor es zu einem Unfall kommt.
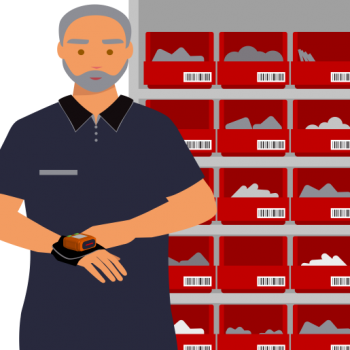
Über Sensoren kann man sowohl Daten von Mitarbeiter*innen als auch zur Arbeitsumgebung messen. So kann eine Software kritische Entwicklungen erkennen und Alarm schlagen.
Zum Beispiel könnten eine zu hohe Temperatur und eine schlechte Luftqualität an einem Arbeitsplatz dazu führen, dass ein*e Mitarbeiter*in Kreislaufprobleme bekommt (erkennbar über die Herzfrequenz) und die Konzentration nachlässt.
Doch problematische Arbeitsbedingungen wirken nicht immer unmittelbar. Arbeitsschutz heißt also nicht nur Schutz vor Unfällen, sondern auch vor Berufskrankheiten. Chronische Rückenschmerzen sind beispielsweise eine Langzeitfolge von dauerhafter einseitiger Belastung.
Sensoren in Schutzkleidung oder in Fahrzeugsitzen liefern Daten, aus denen Algorithmen Anzeichen für eine Fehlhaltung ableiten können. Videoaufzeichnungen der Augen oder Aufnahmen der Stimme können Hinweise auf eine drohende Übermüdung geben. Dann signalisiert das System, dass es Zeit für eine Pause ist.
Aufgabe
Deine Meinung ist gefragt!
Ein Kühlschrank als Coach?
Schon wieder ist die Milch alle! Beim Blick in den Kühlschrank muss Lisa an die Smart Factory denken, in der jedes entnommene Teil gescannt wird und die Software es bei Bedarf automatisch nachbestellt.
Wäre es zu Hause nicht praktisch, einen Kühlschrank zu haben, der erkennt, welche Lebensmittel fehlen, und sie automatisch einkauft?
Andererseits wird Lisa ein bisschen mulmig, wenn sie an die Fähigkeiten eines smarten Kühlschranks denkt. Er könnte ihre Ernährungsgewohnheiten genau überwachen.
Bei ihrem Vater wäre das vielleicht gar nicht so schlecht, überlegt sie, weil er gerade abnehmen möchte. Ein smarter Kühlschrank könnte ihn dann warnen, wenn er zu viele ungesunde Lebensmittel nascht.
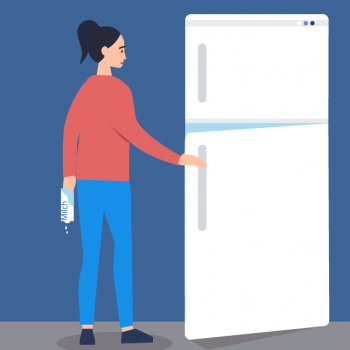
Aufgabe
Was denkst du?